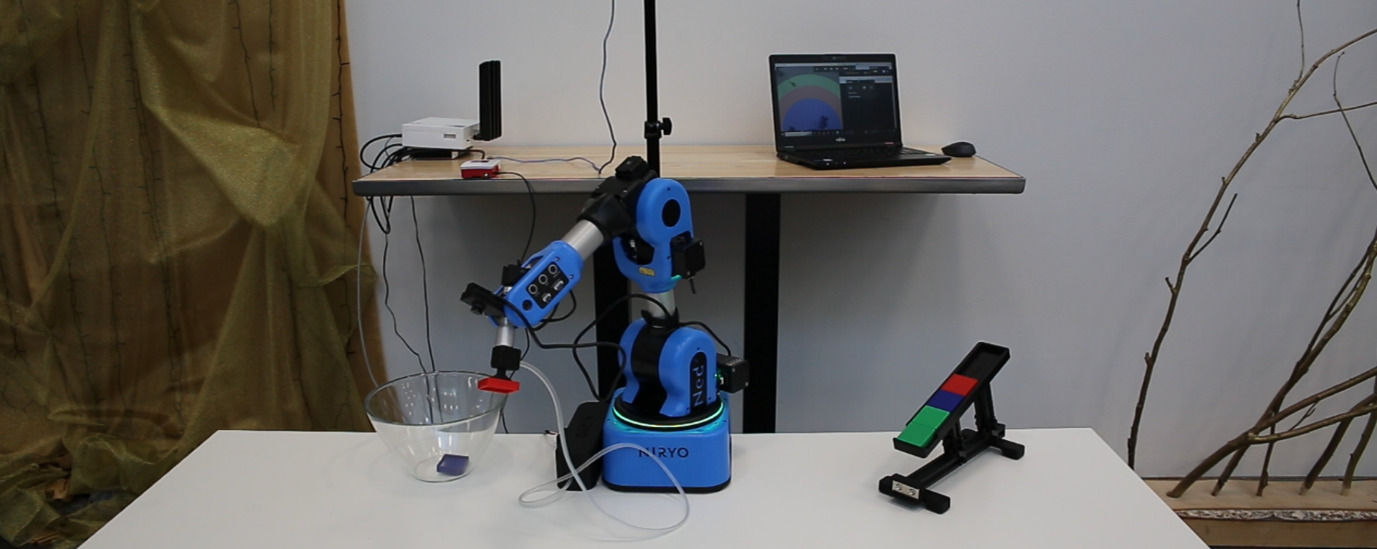
Savonia Article: Safe Zone Application with Arm Robot over 5G network
#SavoniaUAS
In recent years, the use of robots has increased in various fields. With the help of robots, many dangerous and repetitive tasks can be performed more efficiently and with less risk. However, as the number of robots in operation increases, so does the risk of accidents. Therefore, it is essential to ensure the safety of the robots and the people around them. In this context, the concept of safe zone applications has emerged to protect people and prevent accidents.
In safe zone applications, fast reaction is a critical factor in preventing accidents and injuries. When an unexpected event occurs, such as the detection of an object or movement in the safe zone, the robot needs to react quickly to avoid any potential harm to humans or damage to equipment. To achieve fast response times and low latency, a reliable and high-speed network connection is essential. This is where 5G technology shines. With its high-speed data transfer and low latency capabilities, 5G is the most powerful choice for quick response times in safe zone applications. In this study, the use of 5G mmWave network allowed the robot to react with minimal delay, providing real-time information and mission commands to the robot.
Experimental study with Niryo Ned2 arm robot
This is experimental study because current legislation does not allow to use this kind of safety area detection method. In this experiment, a safe zone application was developed using the Niryo Ned2 arm robot and the information was transferred between the robot and the server over the 5G mmWave network. The main goal of this application was to create two circles of safe zones around the robot’s work area. If any object or movement was detected inside the inner circle, the robot would stop immediately. On the other hand, if anything was detected in the outer circle, the robot would enter the alarm state and slow down.

To detect the objects and movements with a 180-degree camera placed on the top of the robot to see the safe areas. The camera transfers the images it obtains with an edge processor to the server. Safe zone areas are scanned with image processing algorithms on the server, motion and object detection are performed in real-time. If anything is detected, this mission commands is sent to the robot and the robot slows down or stops. Robot reacts quickly to the change.
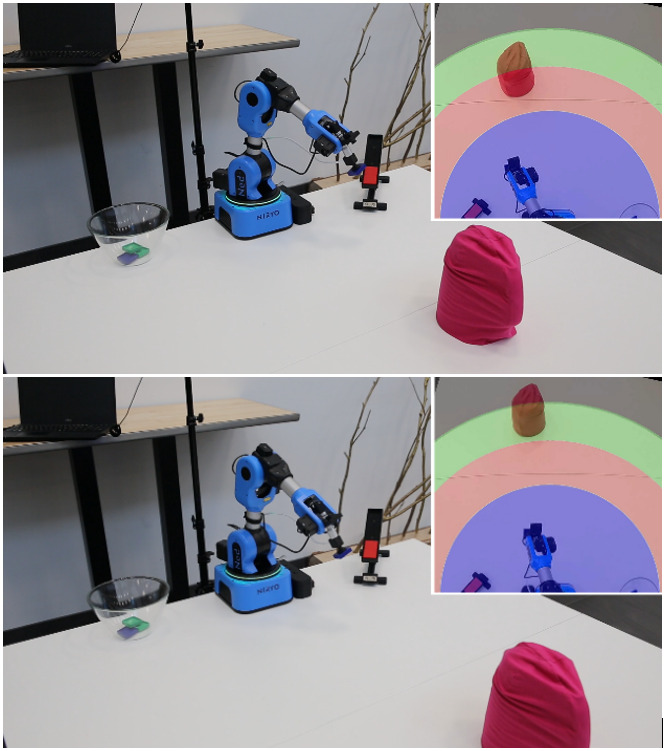
Processing on the edge computing service
The data processing algorithms isn’t performed on the robot itself because the robot isn’t powerful enough to process these algorithms. Therefore, the algorithms are processed on the server and only mission commands are transmitted to the robot. The 5G mmWave network is used to transfer the data between the robot and the server. The 5G mmWave network has high alignment and low latency, making the robot react with minimal delay.
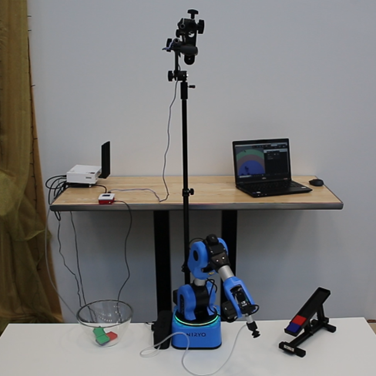
The advantages of 5G network
The 5G mmWave network has several advantages that make it ideal for this application. One of the most significant advantages of 5G is its high speed. The high alignment of 5G enables the transfer of a large amount of data quickly and efficiently. The 5G mmWave network also has low latency, which means that there is a minimal delay between the robot’s actions and the server’s commands. This makes it possible for the robot to react quickly in case of an emergency.
Conclusion
The safety zone application is tested on the Savonia 5G test network. It has been achieved that the use of 5G provides many advantages, including high speed and low latency, making the robot react quickly to any unexpected event. As 5G technology continues to advance and become more widely available, the combination of robotics technology and 5G networks will be used more and more on the high-speed and low latency applications.
Video: https://www.youtube.com/watch?v=1mxx_VYRrQs
Project information: 5G:llä vauhtia digitalisaatioon (REACT-EU EAKR / Pohjois-Savon liitto, A77467)
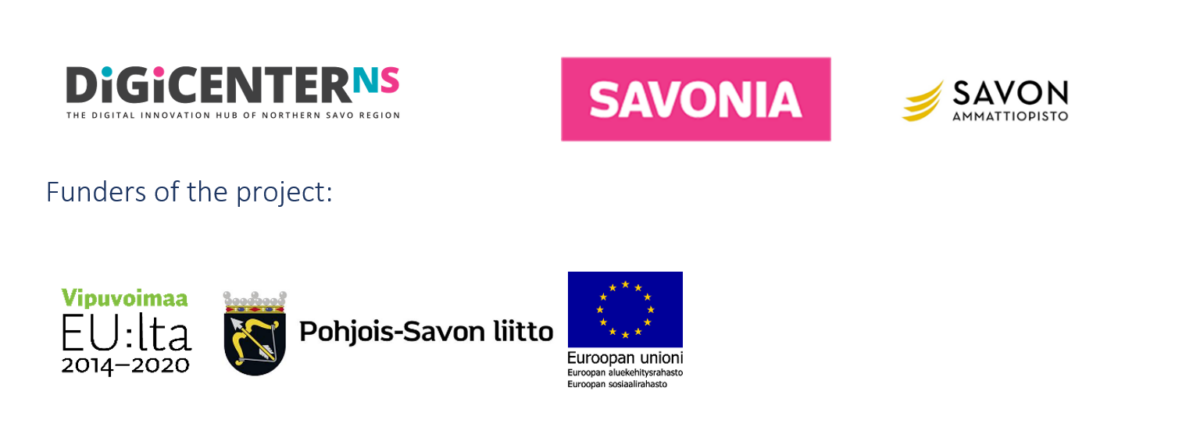
Authors:
Osman Torunoglu, R&D Specialist, DigiCenter, Savonia University of Applied Sciences, osman.torunoglu@savonia.fi
Timo Lassila, Test Engineer, DigiCenter, Savonia University of Applied Sciences, timo.lassila@savonia.fi
Aki Happonen, Project Manager, DigiCenter, Savonia University of Applied Sciences, aki.happonen@savonia.fi